Emergency Action Plan
Purpose and Objective
The company is committed to providing a safe and healthy workplace. This program's objective is to ensure emergency action plans are created prior to work beginning onsite and to prepare employees to deal with them. This will ensure quick, correct, and decisive responses to minimize injury and loss of life. Employees of the company will be informed of this plan and trained to respond to emergency situations.
Definitions
Alarm System: A system capable of alarming employees by being perceived above ambient noise or light levels by all employees in the affected areas of the workplace.
Assembly Point: A previously agreed-upon area near the worksite where employees are instructed to assemble if the work site is evacuated.
Evacuation: The act of exiting a work site in an orderly and expedient manner.
Responsible Person: The employee responsible for managing the Emergency Action Plan. This person shall maintain training records and ensure the plan is kept up to date annually.
Responsibilities
Management is responsible for implementing, supporting, and enforcing this program.
Supervisors are responsible for leading program implementation and ensuring that the safe work practices in this program are practiced. Supervisors are responsible for ensuring that their crew is trained in site-specific emergency action plans and are also responsible for conducting head counts at assembly points in the event of an evacuation. Supervisors are also responsible for ensuring emergency action plans are kept at the worksite and available for employees to review.
Employees are responsible for following the procedures outlined in this program.
Emergency Response Planning, Issuing, and Review
Emergency response procedures are a critical part of maintaining a safe workplace. These procedures will be established, implemented, reviewed, and maintained annually.
Emergency response procedures should be discussed with all new personnel upon arrival and those who have recently transferred. This is to ensure that plans are reviewed before work tasks begin. Changes in operations, products, or services should be updated because they may warrant new emergency response procedures. These procedures should be reviewed with employees regularly.
Emergency response procedures must include a plan for evacuation, including exit routes and role assignments. To implement site evacuation procedures, the following must occur:
- A plan to notify staff of the location and nature of the emergency.
- Evacuation of employees and a plan to safely account for employees.
Plant Layout
A plant layout will be created and posted throughout buildings and plants.
The plant layout includes:
- Assembly Areas (Evacuation)
- Shelter Areas
- Alarm Systems
These maps will be updated when changes occur in the workplace that affect the locations or the suggested evacuation routes. These routes should avoid work areas that may become more dangerous in the event of an emergency such as in front of flammable storage areas.
Emergency Response Equipment
Each site's emergency action plan must identify and list the locations and types of emergency equipment. For off-site locations, emergency equipment should be identified and discussed with employees prior to commencing work activities.
Only trained and authorized personnel should operate emergency equipment. This equipment should include up-to-date inspection and maintenance records. Inspections should be conducted periodically and after each use.
Alarm Systems
- Alarms are used when there is an emergency that requires the entire facility to evacuate or seek shelter. A supervisor will coordinate having an alarm pulled, if necessary. Please see the Plant Layout.
Fire Extinguishers
- Fire extinguishers are located throughout buildings and production areas. Please see attached list.
- Fire extinguishers are also located in heavy equipment, CMVs (commercial motor vehicles), forklifts. Operators are required to inspect their fire extinguishers monthly.
Exit Doors
- Exit doors have exit lights mounted above the door that are equipped with emergency lighting.
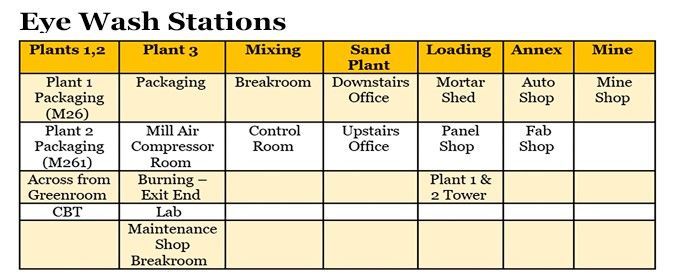

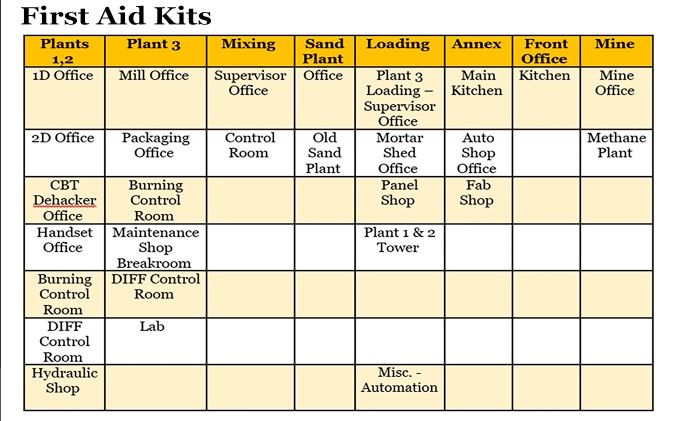
Emergency Response
In an emergency, the person who spots it is responsible for notifying a supervisor. If employees are in immediate danger, the person who spots the emergency must notify those employees prior to notifying a supervisor.
If the employee is to respond by first aid, or fire extinguishers, or any other means, they should first ensure that help is on the way prior to a response.
If the emergency dictates the need for a call to emergency responders, please be prepared to provide as much of the information below as possible:
- Nature of the emergency
- Location of the emergency
- Address, building, room number, etc.
- Your name and the phone number from which you are calling.
- Location of individual needing help (ex., building, column #, parking lot location, etc.)
- After you call first responders, notify a supervisor immediately. A supervisor must wait by the railroad tracks, if safe, to guide emergency responders to the emergency.
Supervisors will use their radio to communicate the nature of the emergency (what type of emergency, location) to other supervisors. Supervisors will also coordinate evacuations, the need to seek shelter via radio. If the entire plant needs to evacuate or seek shelter, alarm systems must be used.
Fire Emergency
In the event of a fire, personnel will follow this procedure:
- Warn others in the immediate area.
- Notify a supervisor.
- Pull fire alarm (if present)
- For staff that are trained to fight fire, and if it is safe to do so, they may proceed with firefighting. We use ABC fire extinguishers.
- All other employees proceed to the exit.
- Group in the emergency assembly area
- Do not re-enter the building until an official has deemed it safe to do so.
Evacuation Procedures
In the event an emergency evacuation is initiated with alarms, total and immediate evacuation of all employees in the affected areas will take place. Three short blasts of the horn indicate an emergency that dictates the need to evacuate to a designated assembly/evacuation area. Assembly/evacuation areas are listed on the Plant Layout.
If the evacuation is localized and does not apply to the entire facility, management will decide what areas are to be evacuated or if they will evacuate the entire facility. This will be dependent on the degree of the hazard.
Evacuations may be required for emergencies such as:
- Fires
- Power failures
- Hazardous materials spill
- Structural damage
- Extreme weather events
- Security issues
- Train derailment
- Propane plant explosion
Supervisors are responsible for guiding their employees during an evacuation. Their duties will include swiftly leading employees from danger to a safe assembly point. Once there, supervisors must ensure safety, must conduct head counts, and must inform emergency crews of anyone missing. Then they will work to provide guidance, ensure that employees stay in place until further instruction, and provide or assist with first aid if necessary. Employees are not allowed to re-enter a facility until it is deemed safe.
After an alarm is sounded to evacuate, the employees should take the following steps:
- Cease work.
- Shut down equipment as required or instructed, if safe to do so.
- Proceed to the nearest safe exit to leave the building or structure.
- Meet at designated assembly point.
- Respond to a roll call.
If an employee is away from his/her regular workstation, he/she should proceed under the direction of the nearest supervisor at the time of the alarm.
Evacuation/Assembly Areas
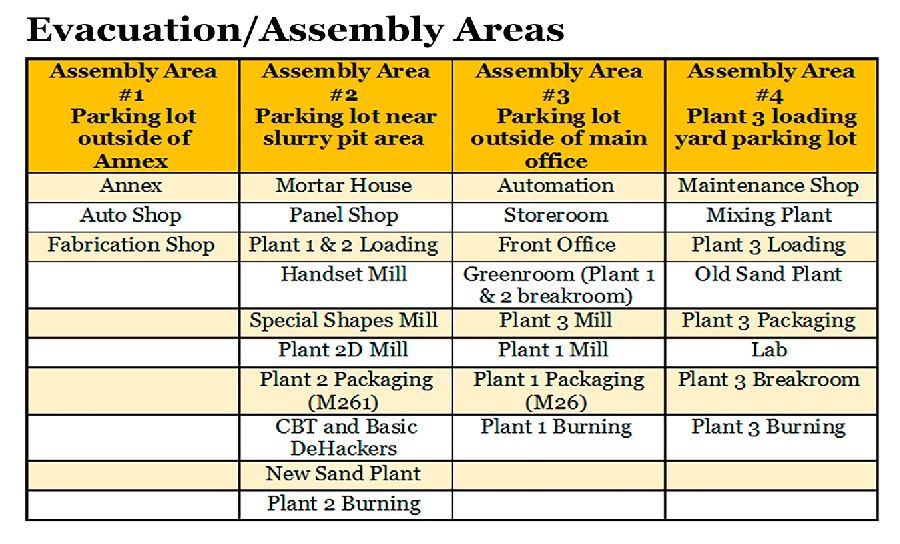
Accounting for Employees and Site Visitors
The company will ensure employees are accounted for in the event of an emergency evacuation by headcounts conducted by supervisors at the assembly/evacuation point in the event of an evacuation. Each supervisor will take a count of employees gathered at the assembly point and inform rescue teams as soon as possible of any missing persons.
Visitors onsite will be accounted for by using sign in/sign out sheets when they arrive onsite. In the event of an evacuation, a sign in/sign out sheet shall be used at the assembly point for ensuring that all visitors are accounted for as well as notifying emergency crews of any individuals who are found to be missing.
Rescue and Medical Duties
In an emergency, it may become necessary to rescue personnel and perform specified medical duties such as first aid. All employees assigned to perform such duties will receive training in first aid and will be properly equipped with PPE (Personal Protection Equipment) and other supplies to carry out their responsibilities safely.
In the event an employee is injured, the first responsibility of any rescuer is to ensure their own safety. Once that has been confirmed, employees are to call the listed emergency contact for help. Report the incident to a supervisor as soon as possible.
Necessary steps should be taken to comfort the victim. Do not move the victim unless necessary for their safety. Utilize employees who are trained in first aid until help arrives.
Critical Operations
In the event of an emergency that would require a facility to be evacuated, select employees who work in critical areas may be responsible for the safe shut down of equipment. The company always considers the preservation of human life and safety to be of the utmost importance. However, when there is no imminent danger, some employees may be expected to take appropriate action to control the emergency. Those individuals will be trained to contain an emergency and will only be instructed to do so if their safety is not in jeopardy.
General Work Procedures
Employees are expected to comply with the following procedures in case of an emergency:
- Assembly points will have been identified by supervisors for all evacuation routes and procedures. These points are designated and posted on each evacuation route. In the event an evacuation is necessary, employees are to use these specified routes.
- Supervisors must report to the designated evacuation points immediately following an evacuation and proceed with a headcount for the employees for which they are responsible. These employees must be accounted for by name.
- Each employee is responsible for reporting to their supervisor in the event of an evacuation so that an accurate headcount can be made.
- Supervisors must report any missing employees to management.
Shelter Procedures
During some emergencies, it may be best for the employee to shelter in place. This will include events such as:
- Earthquakes
- Severe storms
- Thunderstorms
- Tornadoes
- Hurricanes
Safety personnel will check the weather daily. If severe weather is forecasted, safety will monitor the weather frequently throughout the day(s) and update Supervisors, as needed. Safety will notify Supervisors in the event employees need to seek shelter. Supervisors will coordinate shutting down equipment as necessary and getting their employees to designated shelter areas. Shelter areas are listed on the Plant Layout.
If the need to seek shelter is initiated through alarms, all employees must seek shelter in designated shelter areas immediately. A continuous blast of the horn indicates an emergency where shelter shall be sought. Shelter areas are listed on the Plant Layout.
Once in a designated shelter area, crouch as low as possible to the floor, facing down; and cover your head with your hands.
If an employee is away from his/her regular workstation, he/she should proceed under the direction of the nearest supervisor at the time of the alarm.
Shelter Areas
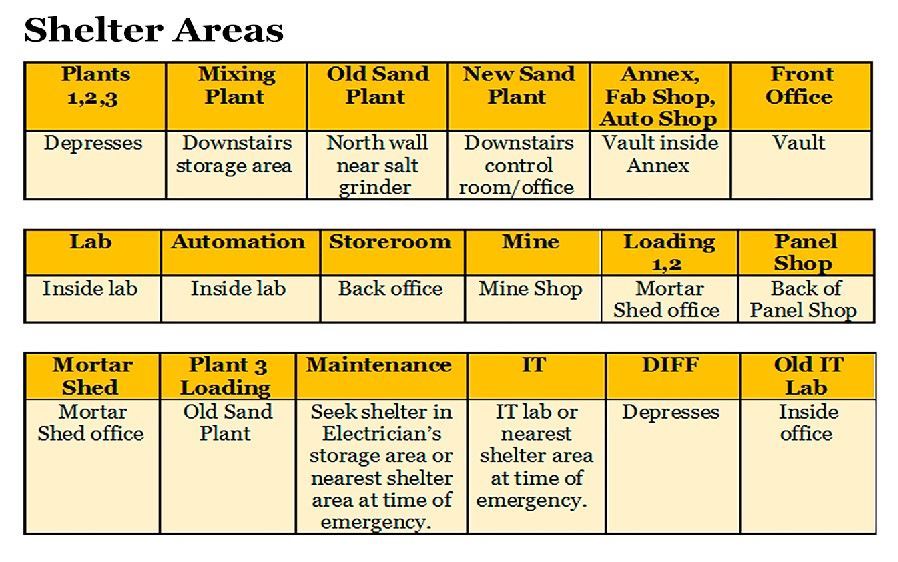
Training
The company will provide training on the emergency action plan for any employee initially upon hiring and yearly thereafter. Training must also be updated for each site the employee works on. The training will include:
- Fire extinguisher use
- Methods to contain spills.
- How to assist other employees or site visitors in evacuating in the event of an emergency
- Evacuation routes and procedures
- Testing of the alarms system
Additionally, training must be conducted whenever an employee’s responsibilities or designated actions under the plan change or whenever the emergency action plan itself changes.
Evacuation drills will be conducted periodically. Training records shall be kept for each employee after training is completed. These documents must be retained for at least three years. The records will include:
- Dates of training sessions
- Contents or a summary of the training session
- Names and qualifications of trainers
- Names and job titles of training attendees
Selected employees may be chosen for higher level responsibilities in the event of an emergency such as the use of fire extinguishers or first aid. Those individuals will be trained based on job assignment and records will be maintained in accordance with all other Emergency Action Plan training records.
Recordkeeping
The company will review this program at least annually to ensure compliance is maintained. Any changes in evacuation routes will be noted and employees will receive the necessary training. The company will maintain records of non-confidential medical evaluation determinations, fit testing, training documentation, and annual inspection audits and will make them available to employees.
IN CASE OF EMERGENCY CONTACT:
CALL 911 FOR FIRE DEPARTMENT/POLICE DEPARTMENT
- WHITLEY MADDOX CELL: (478) 951-8224
(FOR SPILL OR SAFETY/ENVIRONMENTAL EMERGENCIES)
- WILLIE SCOTT CELL: (478) 775-0837
(FOR SPILL OR SAFETY/ENVIRONMENTAL EMERGENCIES)
- MARC AMERSON CELL: (478) 731-5169
- TROY TANNER CELL: (478) 955-5876
- ERIC STEPHENS CELL: (478) 955-9176
- DAVID WARREN CELL: (478) 951-5946
- KATE SAMS CELL: (478) 718-4347
- MIKE PEAVY CELL: (478) 731-6388
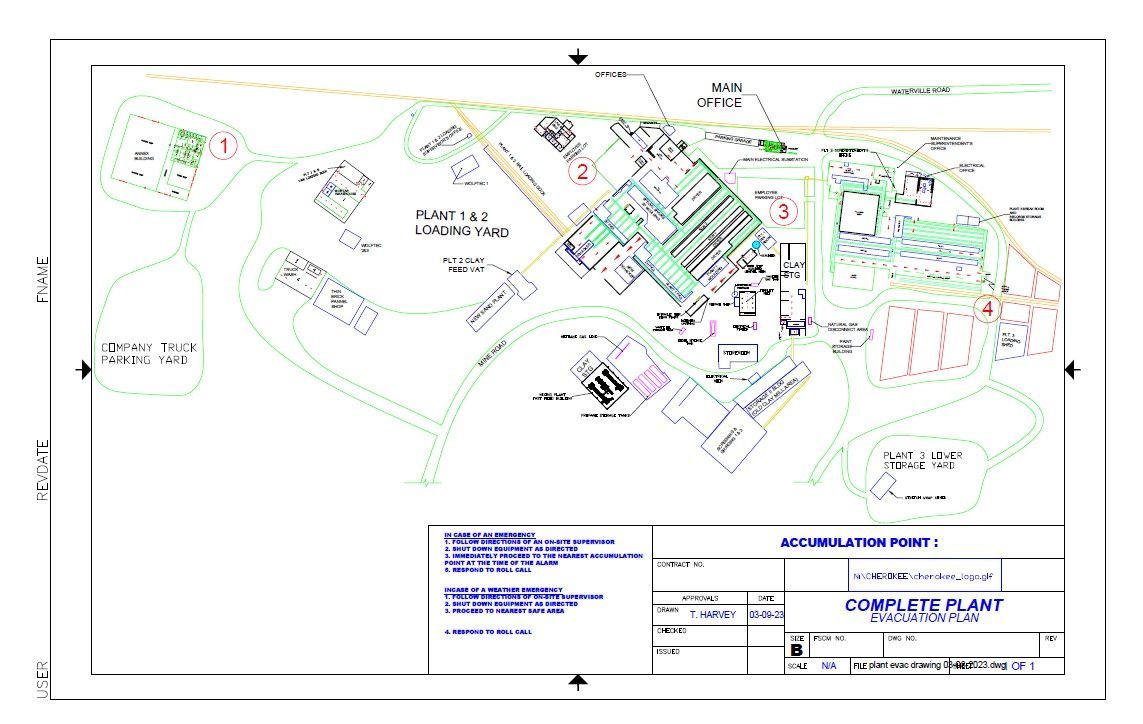